Esta página fue traducida automáticamente.
Complete una encuesta de 1 minuto sobre la calidad de esta traducción.
Calibración del control del par óptimo de un motor PMSM con debilitamiento de campo mediante la calibración basada en modelos
Por Dakai Hu, MathWorks
Calibrar un motor síncrono de imanes permanentes (PMSM) es un paso indispensable en el diseño de controles de tracción eléctrica de alto rendimiento. Tradicionalmente, el proceso de calibración implica extensas pruebas de hardware con dinamómetro (dyno) y procesamiento de datos, y su precisión depende en gran medida de la experiencia del ingeniero de calibración.
La calibración basada en modelos estandariza el proceso de calibración de PMSM, reduce pruebas innecesarias y genera resultados consistentes. Es un flujo de trabajo automatizado probado en la industria que utiliza modelos estadísticos y optimización numérica para calibrar de manera óptima sistemas no lineales complejos. Se puede utilizar en una amplia gama de aplicaciones y es comúnmente utilizado en la calibración del control de motores de combustión interna. Cuando se aplica a la calibración del control de motores eléctricos, el flujo de trabajo de calibración basado en modelos puede ayudar a lograr un control óptimo del torque y del debilitamiento del campo para los PMSM.
Caracterización y calibración de PMSM: Desafíos y requisitos
Los PMSM se distinguen de otros tipos de motores eléctricos por su alta eficiencia y densidad de par. Esto se debe a que los imanes permanentes dentro de la máquina pueden generar un flujo magnético sustancial en el entrehierro sin excitación externa. Esta característica especial hace que un PMSM sea un candidato excelente para aplicaciones de accionamiento de motores de tracción y de no tracción.
La mayoría de las aplicaciones PMSM sin tracción solo requieren que la máquina opere en la región de torque constante, donde su esquema de control es relativamente sencillo. El control de tracción PMSM, además de una respuesta dinámica rápida, también requiere una salida de torque precisa y un funcionamiento en un amplio rango de potencia-velocidad constante. Para lograr estos objetivos de control, particularmente en un vehículo eléctrico o híbrido eléctrico, el PMSM de tracción debe funcionar en el debilitamiento de campo, donde es necesario hacer tradeoffs entre torque, velocidad y eficiencia.
Una gran parte del diseño de un algoritmo de control de debilitamiento de campo de alto rendimiento es calibrar las tablas de búsqueda de control de debilitamiento de campo. Antes de generar los datos de tabla, a menudo es necesario realizar pruebas de caracterización de PMSM utilizando una configuración de dinamómetro o una herramienta de FEA como ANSYS Maxwell o JSOL JMAG.
Después de las pruebas de caracterización del PMSM, se pueden obtener tablas de enlace de flujo y torque medido en diferentes puntos de operación de corriente y velocidad. Aquí es necesario distinguir caracterización y calibración. La caracterización de PMSM implica realizar una serie de pruebas, ya sea en un dinamómetro o utilizando una herramienta de FEA, para extraer información importante, como el enlace de flujo y el torque. La calibración del control de PMSM implica el cálculo de tablas de búsqueda del controlador que generarán el par máximo o la eficiencia óptima en diferentes puntos operativos. El proceso de calibración de control generalmente ocurre después de la caracterización del PMSM. Ambos procesos son necesarios para el diseño de control de PMSM de alto rendimiento.
Flujo de trabajo de calibración basado en modelos
Cuando se aplica a la calibración del control de PMSM, el flujo de trabajo de calibración basado en modelos generalmente implica cuatro pasos (Figura 1):
- Diseño del experimento de caracterización.
- Preprocesamiento del conjunto de datos de caracterización de PMSM.
- Ajuste de modelos de caracterización de PMSM.
- Optimización de datos de la tabla de búsqueda del controlador PMSM.
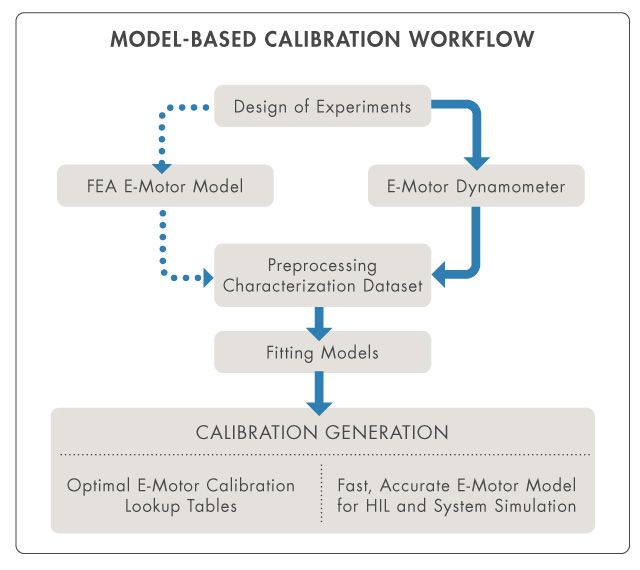
Figura 1. Flujo de trabajo de calibración basado en modelos para la calibración del control de PMSM.
1. Diseño del experimento de caracterización.
La caracterización factorial completa en un dinamómetro físico no es eficiente porque aumenta el tiempo del experimento, el coste y el mantenimiento. En la calibración basada en modelos, se proponen puntos operativos espaciados estadísticamente como puntos de prueba. Independientemente de si el experimento se lleva a cabo en un dinamómetro físico o en un entorno de FEA, los puntos de prueba generados de id e iq actuales se proporcionarán como comandos de control y la velocidad del PMSM será regulada por la máquina dinamómetro o configurada en la herramienta de FEA. El uso de un dinamómetro virtual requiere un modelo de FEA PMSM detallado. Sin embargo, una vez creado el modelo, se puede probar en un conjunto más amplio de puntos operativos sin incurrir en costes adicionales.
2. Preprocesamiento del conjunto de datos de caracterización de PMSM
Durante la caracterización del PMSM, los datos de torque y vinculación de flujo del eje dq se miden directamente en un dinamómetro o se derivan de una herramienta de FEA para cada punto operativo de id, iq y velocidad. Después de la caracterización, el conjunto de datos se reorganiza por contornos de torque y pasos de velocidad, y cada variable (por ejemplo, torque) se almacena en un formato de una sola columna, que luego se importa a Model-Based Calibration Toolbox™ (Figura 2). Si es necesario, se pueden realizar análisis adicionales para eliminar datos atípicos. Los valores atípicos son comunes durante las pruebas físicas debido al ruido y al error de medición.
3. Ajuste de modelos de caracterización de PMSM
El ajuste del modelo es una parte fundamental del flujo de trabajo de calibración basado en modelos. (Tenga en cuenta que los modelos a los que se hace referencia en este artículo no son modelos de motor o controlador eléctrico; son modelos estadísticos en los que funciones como la regresión del proceso gaussiano o la función de base radial representan la relación entre variables en el conjunto de datos importado). En concreto, se crean dos conjuntos de modelos: iq en función de id y par, y margen de tensión en función de id y par. Cada uno está modelado en un conjunto común de velocidades de motor. Estas velocidades se utilizan como puntos de interrupción para la tabla de búsqueda del controlador final. La figura 3 muestra modelos agrupados por dos puntos de operación de velocidad: 1000 rpm y 5000 rpm.

Figura 3. Ejemplos de modelos de Iq y margen de voltaje (delta_vs) en diferentes puntos de operación de velocidad.
Los modelos de margen de voltaje y de iq varían según los puntos de operación de velocidad, ya que la velocidad puede afectar directamente el límite de operación. Es imposible representar con exactitud el límite de operación a partir de un número finito de puntos de datos caracterizados. Los límites de funcionamiento reales del PMSM bajo calibración a menudo están impuestos por factores limitantes externos, como el límite térmico del sistema de accionamiento y el nivel de voltaje del bus de CC del inversor.
En la calibración basada en modelos, los límites de operación de los modelos ajustados se aproximan mediante las envolturas convexas que encierran el conjunto de datos, como lo representan los bordes de las superficies coloreadas en la Figura 3. Estos límites son importantes para el paso 4 del flujo de trabajo de calibración, ya que se utilizan como restricciones para el problema de optimización.
4. Optimización de datos de la tabla de búsqueda del controlador PMSM
En la calibración basada en modelos, el proceso de ejecución de rutinas de optimización y generación de las tablas de búsqueda de calibración finales se realiza utilizando CAGE, la herramienta de generación de calibración de Model-Based Calibration Toolbox. En CAGE, los modelos del paso 3 se utilizan para modelos de función objetivo o como restricciones. Por ejemplo, los modelos de margen de voltaje se utilizan como restricciones de voltaje a diferentes velocidades para garantizar que el voltaje de modulación general no exceda el máximo impuesto por el voltaje del bus de CC. Además de las restricciones, también se pueden establecer objetivos individuales o múltiples en función de estos modelos ajustados.
Un objetivo común para el control optimizado del debilitamiento de campo es maximizar la eficiencia del PMSM mientras se alcanza el par requerido. Esto se logra estableciendo el torque por amperio (TPA) como el objetivo para maximizar y aplicar simultáneamente las restricciones de corriente y voltaje. El resultado es una región de operación optimizada que cubre el máximo par por amperio (MTPA), el máximo par por voltio (MPTV) y puntos de operación intermedios.
La figura 4 muestra cómo se obtiene un punto de operación optimizado en la tabla de búsqueda a través del proceso CAGE. Las áreas sombreadas de color azul claro y amarillo representan las restricciones de corriente y voltaje correspondientes en un punto operativo de velocidad específico, siendo el área verde la región viable que satisface ambas restricciones. El contorno de torque en el gráfico representa un requisito de torque específico. Para lograr el máximo control de eficiencia del PMSM, el optimizador en CAGE busca a lo largo del contorno de torque dentro de la región viable para encontrar un punto que maximice el TPA objetivo. Como resultado, en el ejemplo mostrado en la Figura 4, el punto A será elegido como el óptimo. Los demás puntos de la tabla de búsqueda optimizada en la Figura 4 se calculan mediante la misma rutina en CAGE.
Puede acelerar la rutina de optimización descrita anteriormente ejecutándola con Parallel Computing Toolbox™. Con cálculo paralelo, todo el flujo de trabajo converge en menos de 10 minutos en una PC típica de cuatro núcleos.
Después de ejecutar la rutina de optimización, puede completar las tablas de búsqueda de calibración final con los resultados de optimización a través de varios métodos de relleno, como interpolación o recorte. En teoría, puede elegir cualquier punto de interrupción de torque y velocidad para la tabla de búsqueda, pero una elección común de puntos de interrupción para el torque es el porcentaje del torque máximo. Cuando se elige un porcentaje de torque del torque máximo alcanzable en lugar de valores de torque absolutos se garantiza que toda la tabla de búsqueda se rellene con resultados de optimización válidos (Figura 5).

Figura 5. Tablas de calibración de id y iq optimizadas con debilitamiento de campo incluido.
Extensión del flujo de trabajo
Este artículo cubrió el flujo de trabajo de calibración basado en modelos básicos para la generación de tablas de búsqueda de control de torque PMSM óptimo con debilitamiento de campo. El ejemplo descrito en el artículo se basa en tablas de control de debilitamiento de campo donde el comando de torque, la velocidad y posiblemente el voltaje del bus de CC son entradas.
Para un algoritmo que utiliza el comando de torque y el enlace de flujo máximo como entradas a sus tablas de búsqueda, el flujo de trabajo es el mismo, solo que con modelos de función ligeramente diferentes. Además, si su aplicación requiere una calibración más precisa y refinada, puede considerar más variables, como la caída de voltaje del inversor, la pérdida del núcleo, la resistencia de CA y el viento o la fricción, durante el ajuste del modelo y el proceso CAGE.
Publicado en 2020