Lockheed Martin Space Systems Uses a Real-Time Simulator to Automate Mars Reconnaissance Orbiter Development
"Simulink, Simscape Multibody, and Simulink Coder enabled us to autonomously go from an accurate CAD model of the MRO vehicle into C code that runs in real time."
Challenge
Solution
Results
- Spacecraft pointing simulation modeled in days
- Interorganization communication improved
- Efficient code generated automatically
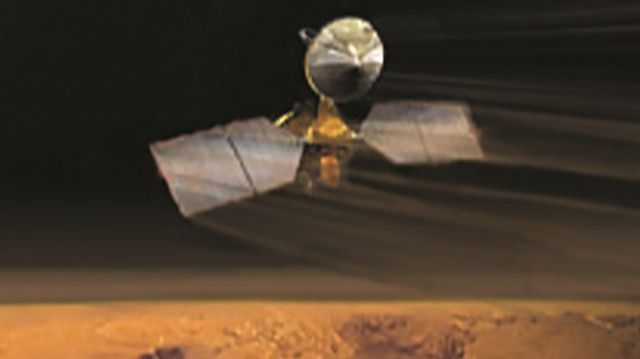
Did water on Mars persist long enough to provide an environment capable of supporting life? In 2006, scientists will be closer to answering that question when the Mars Reconnaissance Orbiter (MRO) begins sending them high-resolution images and other data collected by the most advanced instruments and cameras ever sent to the Red Planet.
To provide a stable platform for obtaining images with unprecedented clarity, Lockheed Martin Space Systems Company used MathWorks tools for Model-Based Design to develop a guidance, navigation, and control (GN&C) system to simultaneously align the high-gain antenna to Earth, track the Sun with the solar panels to collect power, and orient the cameras toward surface features on Mars.
"The MRO design was based on a library of modules written with MathWorks tools that we have been evolving since the Mars Global Surveyor program of the 1990s," says Jim Chapel, Ph.D., lead attitude control engineer at Lockheed Martin Space Systems Company. "We can confidently reuse verified modules on projects, which is a big advantage in terms of reducing development costs."
Challenge
With surface resolution as small as 25 cm, MRO cameras can detect objects the size of a basketball on the surface of Mars. To support such high-resolution imaging, the MRO’s GN&C system must provide an extremely accurate and stable camera platform while constantly repositioning its solar panels and three-meter, high-gain antenna.
To verify the control design, the MRO team needed to develop an accurate simulation of the spacecraft. "Writing closed-form equations for the dynamics of the MRO is extremely complex because it is a multibody system. We needed to automate the development of those equations of motion for efficient simulation," Dr. Chapel explains. "We wanted to translate mechanical models of the spacecraft developed in CAD software into an accurate mechanical dynamics model using a repeatable, reliable, and automated process."
Solution
Lockheed Martin engineers used MathWorks tools to design and simulate the GN&C system for the MRO and to automatically develop a real-time simulation model of the spacecraft, which originated from a CAD mechanical model.
The team used MATLAB and Simulink to develop the algorithms and associated parameters for the MRO’s GN&C system, which incorporates input from sensors, including inertial measurement units, star trackers, and sun sensors, and drives reaction wheels and gimbals to point the spacecraft and its appendages.
Over the past several years, the team has used Simulink and Simscape Multibody™ to assemble a library of models for spacecraft actuators, sensors, control algorithms, and vehicle dynamics. They used this library to rapidly develop high-fidelity models of the MRO spacecraft, including flex and fuel slosh modes. Because the MRO spacecraft model and the controller model are in Simulink, the team efficiently simulates the control system and determines thousands of control parameters for various mission phases and operational scenarios. The control parameters developed in Simulink were directly loaded into the spacecraft parameter database.
Lockheed Martin engineers also used Simulink, Simscape Multibody, and Simulink Coder™ to develop the Orbiter Test Bed (OTB) for real-time, hardware-in-the-loop (HIL) simulation of the MRO. Engineers used the OTB HIL tests to verify the flight software prior to launch and continue using the OTB to verify all commands and sequences during operations.
The team has automated the process of generating mechanical models in MSC.ADAMS from CAD models. Because the standard multibody dynamics description of the body, joint, and coordinate systems in ADAMS matches the modeling description of Simscape Multibody, Lockheed Martin readily translated the ADAMS model into Simulink through Simscape Multibody. They then used Simulink Coder to automatically generate C code from their Simulink models to implement high-fidelity dynamics models in the OTB HIL testing.
During the seven-month journey to Mars and throughout the mission, Lockheed Martin engineers used the OTB to verify GN&C performance. The team is also using Signal Processing Toolbox™ to analyze accelerometer data from calibration and jitter tests conducted onboard the MRO.
Results
Spacecraft pointing simulation modeled in days. "Using MathWorks tools and our library modules, we can build a reasonably accurate simulation model of spacecraft pointing in less than a week or a couple of days. The stability and pointing capabilities of the MRO are within the original estimates made using our initial model," says Chapel. "These libraries accelerate our development schedules and provide us with a high degree of confidence in the end result."
Interorganization communication improved. "Because we are all using MathWorks tools, we can exchange models and analysis tools with our primary customer, NASA’s Jet Propulsion Laboratory," reports Chapel.
Efficient code generated automatically. "Using Simscape Multibody and Simulink Coder to automate the process of developing the OTB HIL simulation enabled us to produce high-fidelity simulations requiring less than 1 millisecond of the 10 millisecond OTB HIL simulation frame," notes Chapel.